All-in-one closed-loop linear positioning: AMP launch compact linear actuator with StepSERVO™ integrated motor + drive + motion control
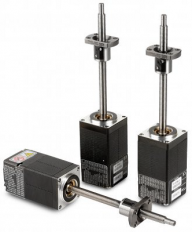
New from USA motion control specialists Applied Motion Products (AMP) and available from Mclennan, NEMA size 11 StepServo™ integrated motors are now available as compact all-in-one linear actuators fitted with precision ballscrew or leadscrew output shafts and anti-backlash nuts. As a convenient and costeffective drop-in solution the new TBSM11 linear actuator includes the positioning mechanics, servo drive, motor, feedback and motion controls that are required for a variety of high precision linear positioning and force/tensioning tasks.
AMP’s StepServo extends closed-loop servo performance to traditional stepper motor based motion systems with ‘integrated motor’ packages that include microstepping motors with built-in drives, encoder feedback, motion controllers and optional fieldbus communications. Highly developed servo control algorithms provide up to 50% more torque than normal steppers with significant benefits including higher precision control, higher acceleration, faster machine cycles and greater productivity as well improved energy efficiency and quieter operation.
For the current TBSM11 series AMP has used its miniature NEMA size 11 motor which has a nominal torque around 8 Ncm that provides around 100 N of usable force for the actuator (based on a 5 mm pitch ballscrew). With screw pitches from 1 mm to 5 mm/rev and repeatability to ±0.02 mm users can choose ballscrew or lead screw solutions with diameters up to 6 mm.
Mclennan’s sales and engineering team are able to specify the optimal screw and mating nut solution with stroke length, end machining and nut preloading designs. From a mechanical installation perspective, the TBSM11 reduces design effort, saves space and removes the need for couplings whilst directly offering a typical closed-loop positioning resolution to 0.005 mm per motor step. The use of an integrated motor solution also means less wring and an easier and altogether more compact installation.
The TBSM features on-board motion control with AMP’s Q Programming software which allows operation as a stand-alone axis with motion profiles stored in non-volatile memory. Software supported set-up, configuration, programming and firmware management is via an RS-485 communication port that also enables network connections for multiple axes.
The comprehensive StepSERVO range is available in a wide selection motor powers and sizes from NEMA 11 through to NEMA 34 frame motors. Motion control options include pulse or analogue control as well as a choice of built-in Modbus/RTU or CANopen multi-axis networking. Pre-programmed stand-alone operation using AMP’s ‘Q’ motion software and Ethernet based fieldbus’ including EtherCAT is also available.
Mclennan supports the complete range of StepSERVO, DC servo intelligent drives, separate stepper and servo drives, motors and other motion components from AMP which offer similar levels of control where all may be mixed for complete and competitively priced multi-axis motion and machine control system solutions.